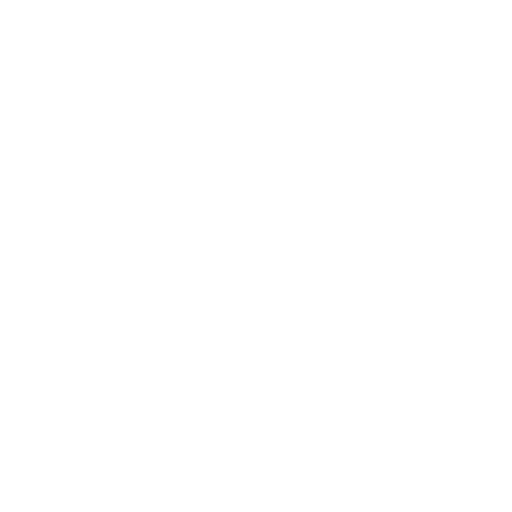
Building design: Box gutters – friend or foe?
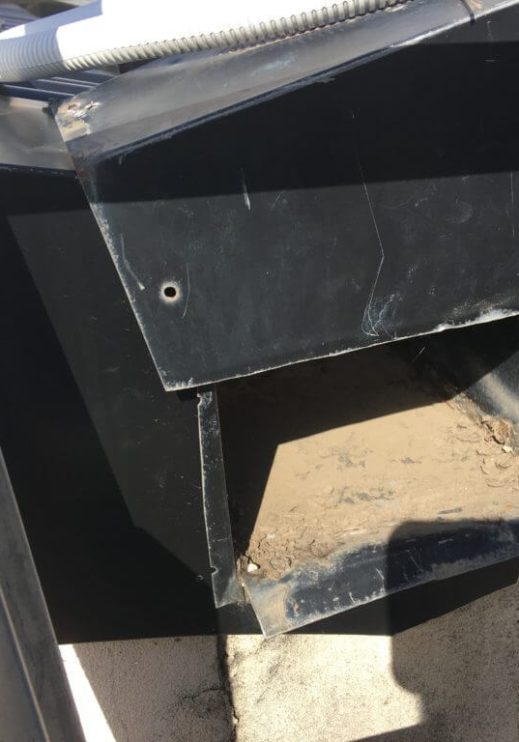
Are you considering building your new dream home? If so, I’m sure you have done the rounds looking at display homes, checking out magazine and internet articles, talking to friends and neighbours and have found ‘the look’ you want your house to have.
A lot of current home designs tend to incorporate a decorative parapet to some degree into their façade.
What generally makes a parapet styled façade possible is a box gutter.
So what is a box gutter?
A box gutter is typically rectangular in size and concealed from view behind a parapet or other elements, eg high-sided fascia board. The gutter collects rainwater from any roof and wall surface ‘up hill’ from its position and discharges to a drainage system.
The use of box gutters has allowed building designers a much greater range of façade design possibilities and pleasing aesthetics.
Like many things, box gutters can be done right and wrong.
So what happens when a box gutter is not designed or constructed correctly?
Box gutters due to their nature are a concealed item, usually over an habitable room or area and above surface finishes that don’t take kindly to moisture, like that beautiful plasterboard ceiling.
Usually you are first aware that something is amiss when the box gutter fails or leaks, staining and/or damaging surfaces below.
What makes a good box gutter?
The Building Code of Australia (BCA) and Australian Standard 3500.3 (stormwater design) provide minimum design criteria, which generally are based on property location, average rainfall and style of construction.
A very important element to any box gutter is a safety overflow system. I am constantly surprised at the number of box gutters I see which don’t have any additional means to discharge rainwater collected, ie safety overflows.
The risk of water entry within a building due to the blockage of a box gutter during extremely heavy rainfall is increased if any trapped or high volume water has nowhere to escape, apart from a path of least resistance, over the sides of the box gutter and inside the building.
Material selection is also important. Best building practice is to select the most durable and cost effective material.
Although initially a little more expensive than other commonly used materials, stainless steel is, in my opinion, the only choice.
The use of stainless steel removes one of the biggest contributing factors of premature failures in box gutters – corrosion.
Box gutter maintenance
Like all building elements regardless of material selection or position, box gutters will require regular maintenance to minimise risk of water entry
This includes regular inspection and removal of any debris build-up or any items within the gutter and safety overflow, such as leaves, branches, tennis balls/basketballs, birds nests, building debris, etc that could led to a blockage and/or restrict water movement.
Don’t be tempted to fit a leaf guard style product over a box gutter as this can, and usually does, lead to water entry, not generally due to box gutter failure but due to the profile of the roof covering above.
Briefly, when leaf debris builds up where the gutter guard is fixed to roof surfaces it creates a ‘damming’ effect and the ponding water can gain entry over joins in the roof covering.
If gutter guard has to be fitted, special consideration is required in relation to positioning and allowance for the guard during the initial design process
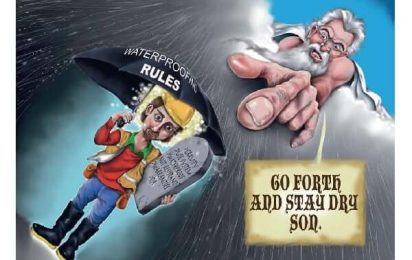
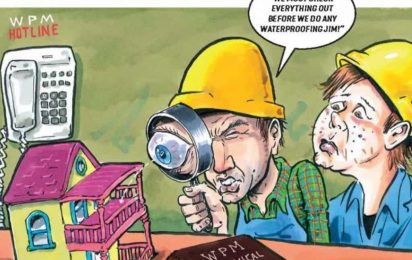
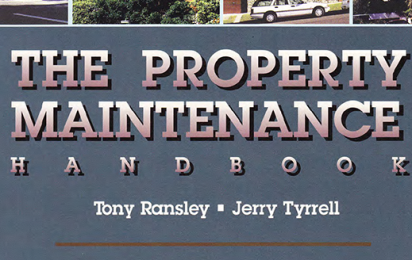
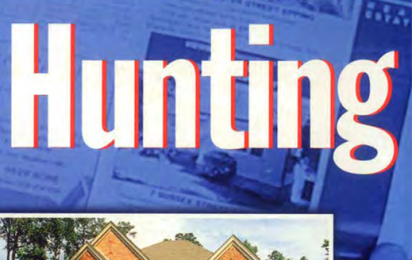

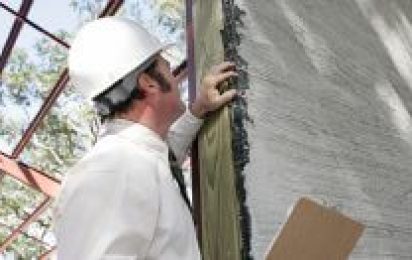
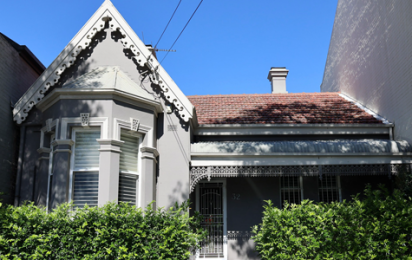
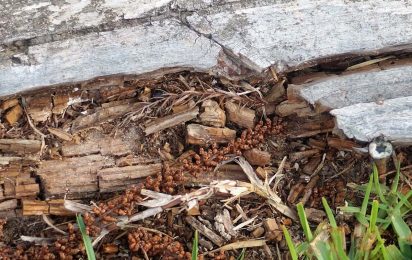
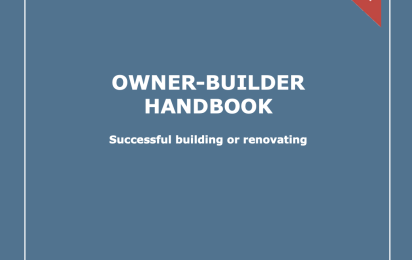
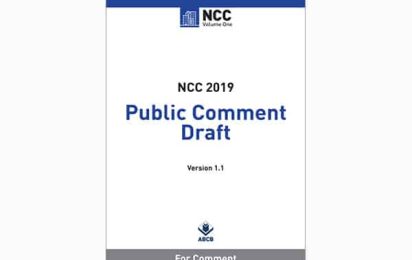
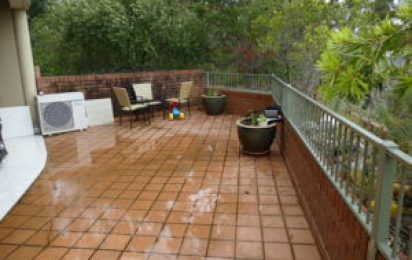
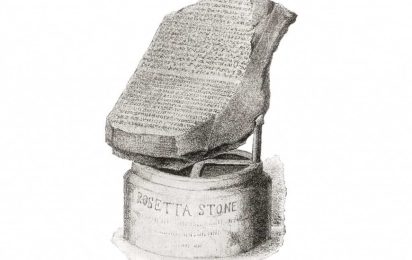
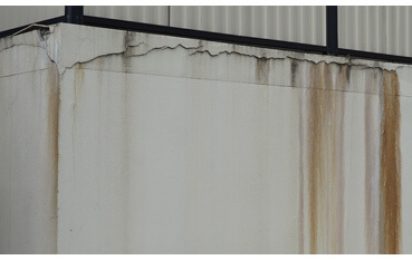
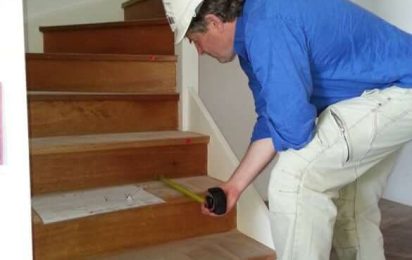
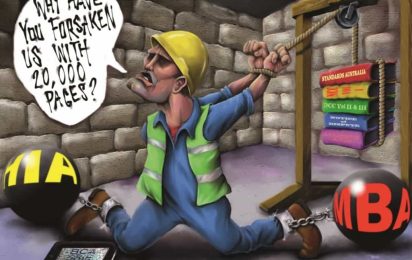
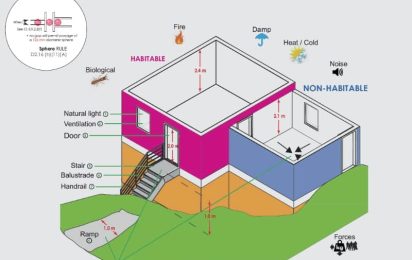
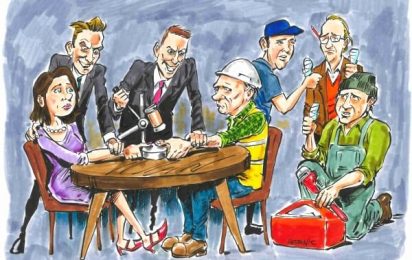
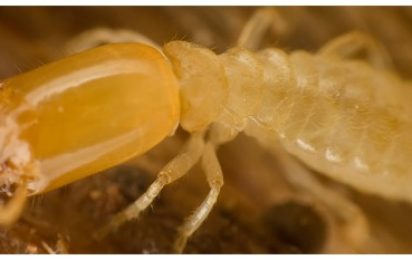
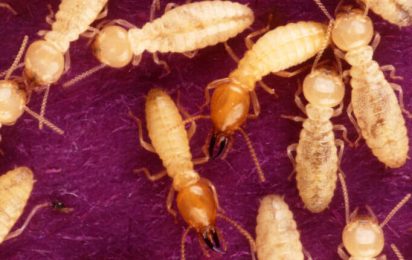
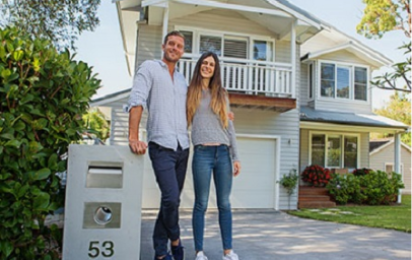
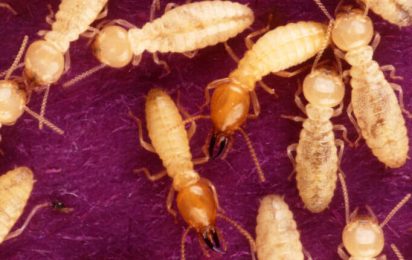
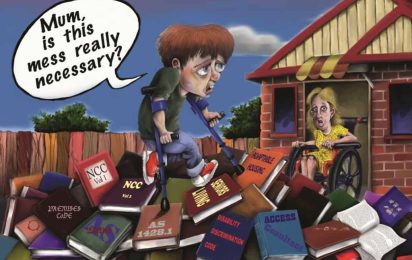
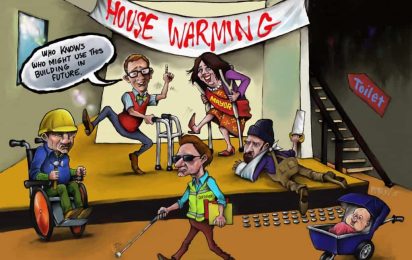
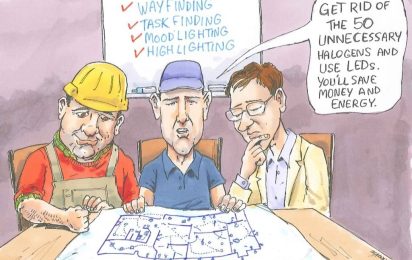
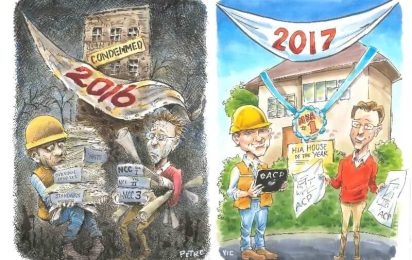

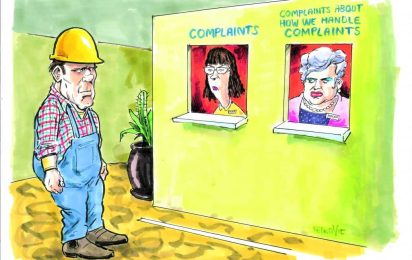
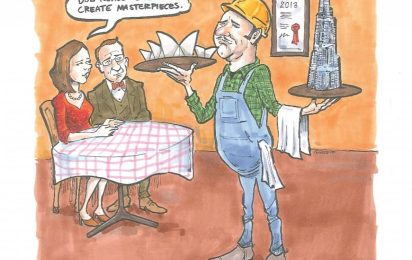
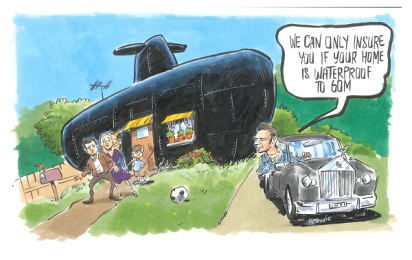
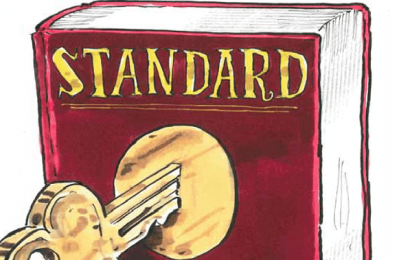
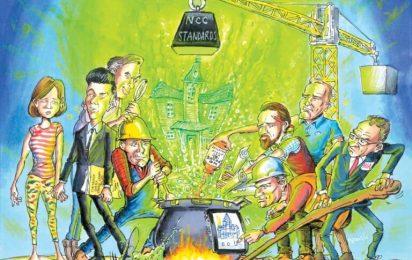
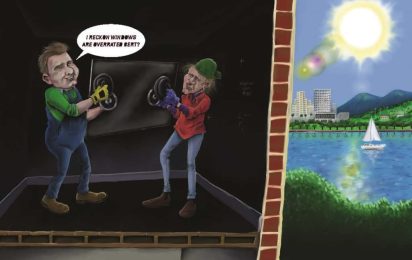
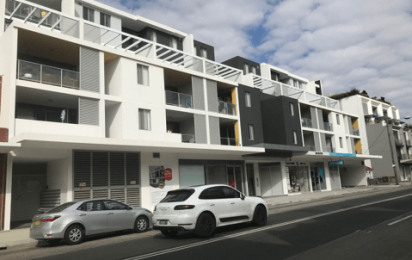
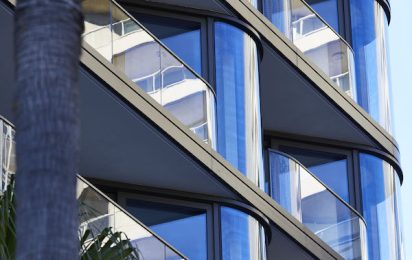
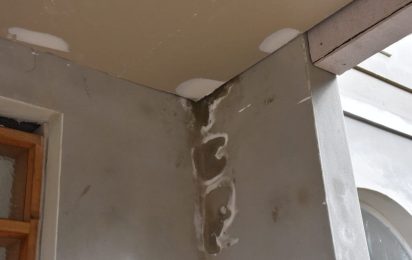
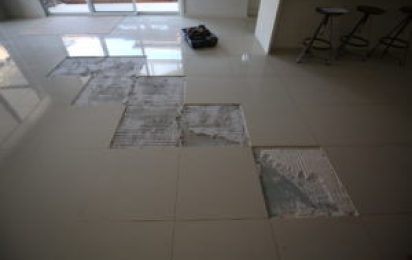
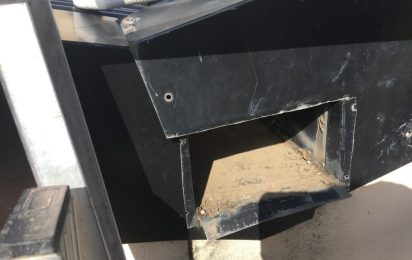
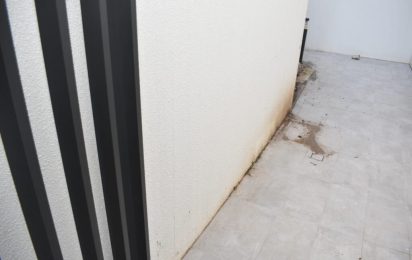
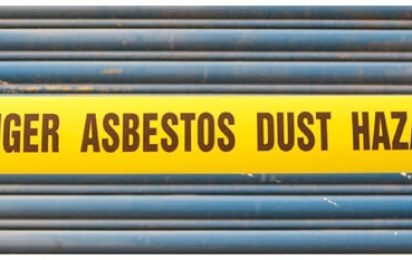
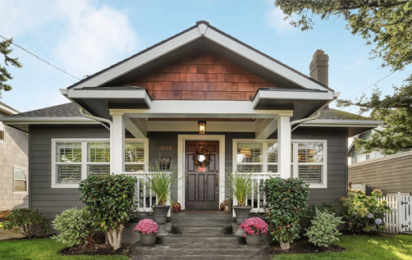
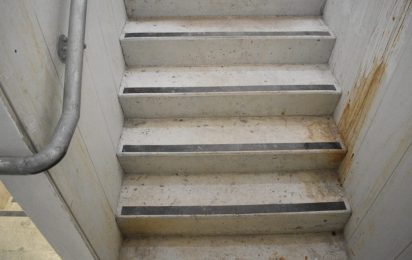
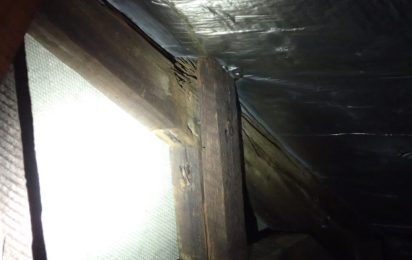
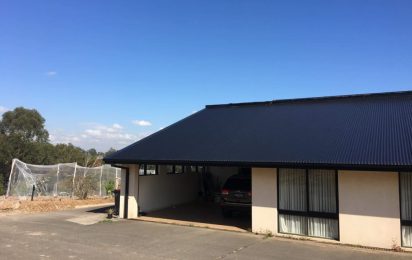
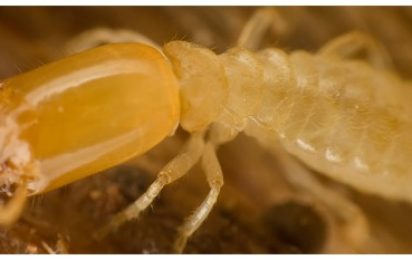
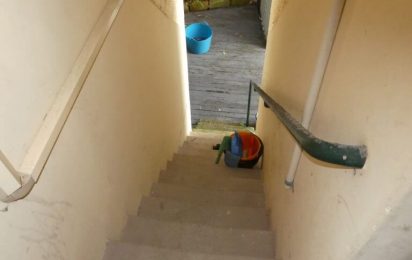
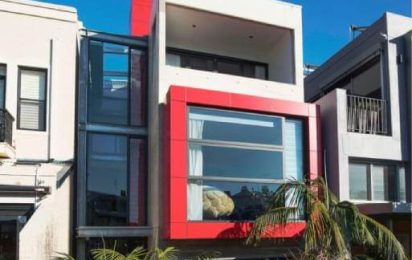
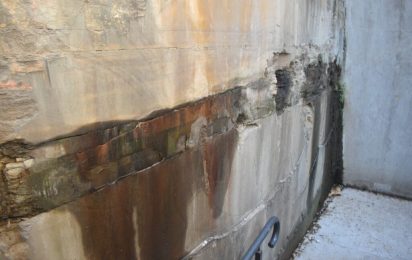
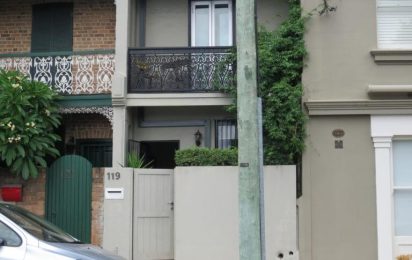
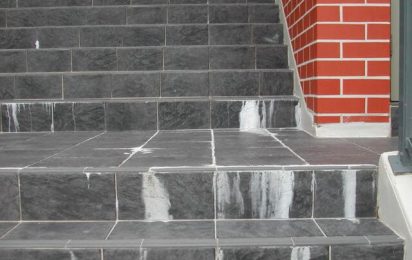
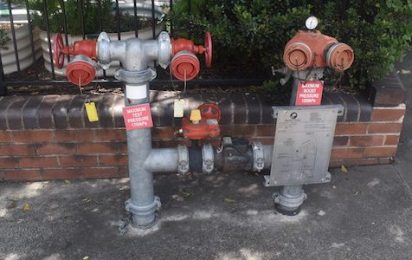
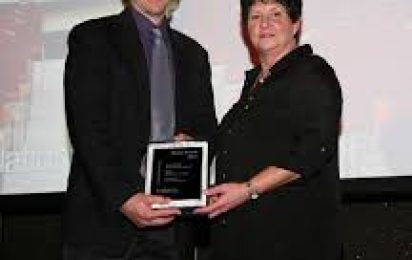
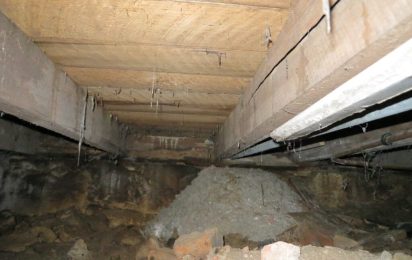
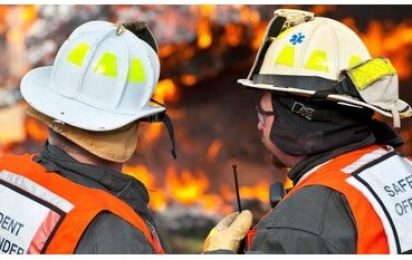
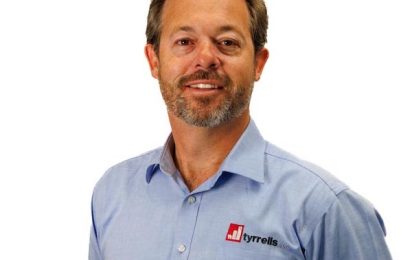
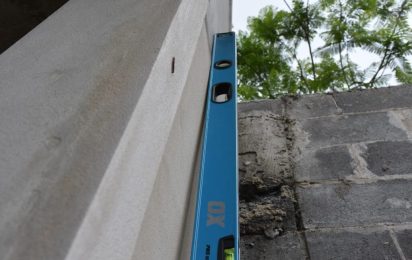

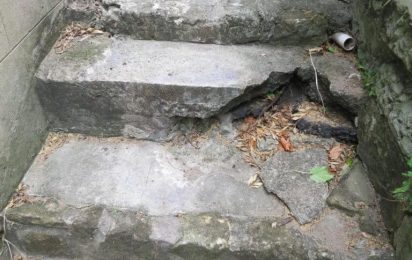
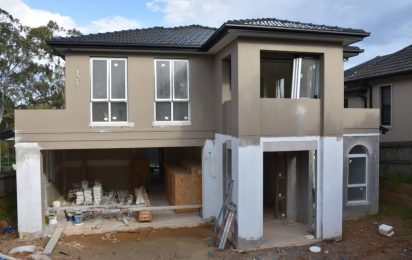
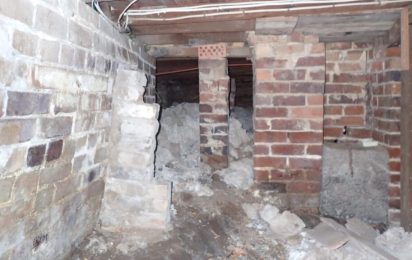