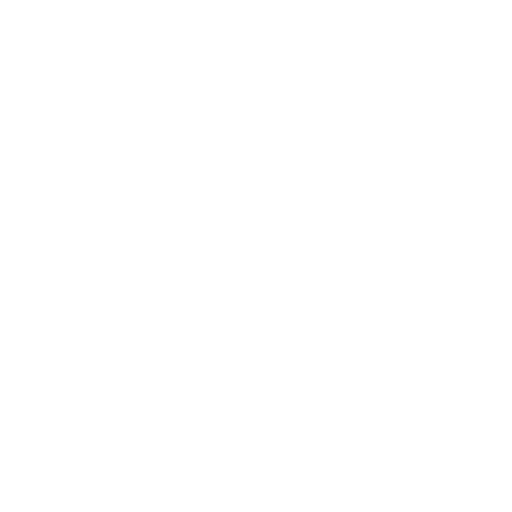
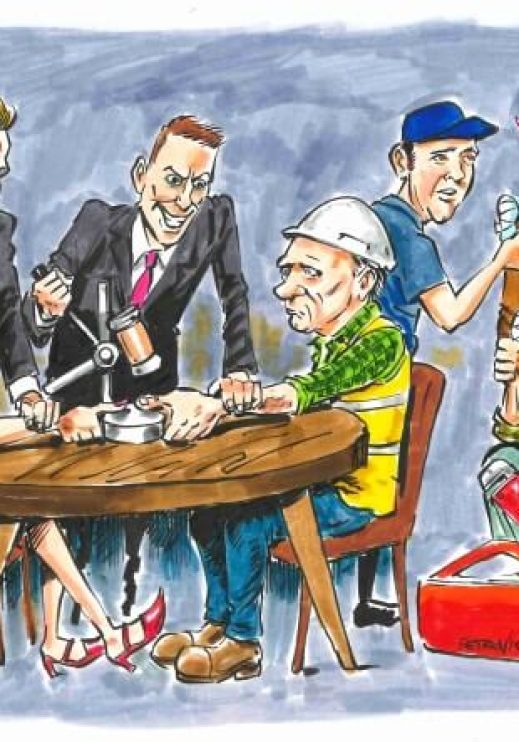
Jerry Tyrrell explains what ‘we’ need to do… because no else will.
I’ve been watching our industry for nearly 50 years. Mistakes cost us a fortune every year. I reckon we waste over $5b on rectification or maintenance work we don’t like doing. This money could be spent on schools and hospitals. Most problems I see are unintended and caused by ignorance.
I am convinced the best way to build is to build properly – using materials and techniques that work. It should be easy. And it would be if a few simple changes were made.
Quality stops unreasonable criticism. Products that are durable and easy to maintain keep our customers happy. Greedy lawyers cannot beat up a dispute if our mistakes are small and we are allowed back on site to fix them. And architects and designers need to stop blaming us. They are better off telling clients that good building work costs more than they expect and that it’s often better to make a few changes during the work even if it costs a bit more.
But not a lot is changing.
Sure, a few smart builders use a serious quality process to limit post completion issues. However, most of the time we still allow mistakes to cause expensive call backs or, at worst, life changing disputes. Or our work costs a lot more to maintain than it should. Or parties just fight about issues that always happen in building work. So what are you going to do about it?
I have never hit my thumb with a hammer. I don’t need to know how much it hurts. I have listed a few solutions below for you to target as you know that change will only happen if you make it happen.
Problem | Solution |
Insurance | |
Excessive cost | Cost will be reduced if contractors do not make unintentional mistakes. |
Confusing process | Contractor must be allowed to fix his/her mistakes. |
No significant benefit | Why not have free insurance and only penalise a contractor with a premium when they fail to build properly or fix a mistake? |
Product quality | |
Suppliers are not responsible for their product | Governments should require manufacturers to take primary responsibility for serious failure and faults. Like a toaster or a car – the manufacturer has to fix it, not the person selling it. |
Product warning | |
No clear intel about how to use it | All products should have durable hazard warnings and QR codes. |
Life safety products eg. fire doors, linings, termite barriers etc. should have permanent durable signage. | |
Latent defects in existing buildings | |
Rarely do clients and builders look for the serious problems before renovating or adding to the building eg. termite damage, rising damp, rotted windows, basement dampness etc. | Client / architects must provide a condition report on older buildings. |
Cost overruns | |
Clients underestimate cost of their work | The industry should publish the average extra costs consumers experience (minimum 15% including variations and extras). |
Confusion over variations and extras | Designers should warn consumers that these should be expected. |
Compliance | |
Confusion over best practice and how to quickly access what is required | NCC and Standards are working on improving access. It needs to be diagrams available on your laptop or phone. |
Quality Assurance | |
Confusion over who is responsible | Blame will stop if we sort this out. Everything we do needs to be inspected. And you know what? We are the best ‘inspectors’ if we know what we’re doing and provide the certification from competent colleagues. |
Critical maintenance | |
Confusion over what should be done and when | Timber sills, box gutters, pool gates, garage doors and the like all require maintenance. But instructions should be left on the product, for example: Termite Barrier: Do not obstruct. |
Financial risk | |
Contractor’s business can be affected if a client decides not to pay final claim | This is so silly. The profit is in the final claim. Often clients use petty nonsense to delay payment. Or have run out of money because they never had enough for the 15% extra work that they wanted. Payment guarantees must be put in place. |
Feedback | I regularly meet contractors and designers who simply don’t know about a known problem, such as the use of MDF in basements/front doors, plasterboard used for external soffits, dogleg valleys, floor level set out around stairs etc. Why doesn’t Australia have a central resource that sends alerts out to us? |
CPD | CPD should include the above alerts plus access to what we all need – easy to apply drawings of compliant best practice. And we need yearly updates of changes to safety and workplace rules. This can be positive too. Here’s an example: ALERT: Cordless technology reduces electrical hazards on your site. |